无心磨削是工件不定中心的磨削,主要有无心外圆磨削和无心內圆磨削,如下图所示。外圆磨削时,工件2安置在磨削轮1与导轮3之前,由托板4托住下部,磨削轮起磨削作用,导轮带动工件旋转并推动工件靠近磨削轮。內圆磨削时工件2安装在导轮3、支承轮5、压紧轮6之间,工作时导轮起传动作用,工件以与导轮相反的方向旋转,磨削轮1对工件内孔进行磨削。
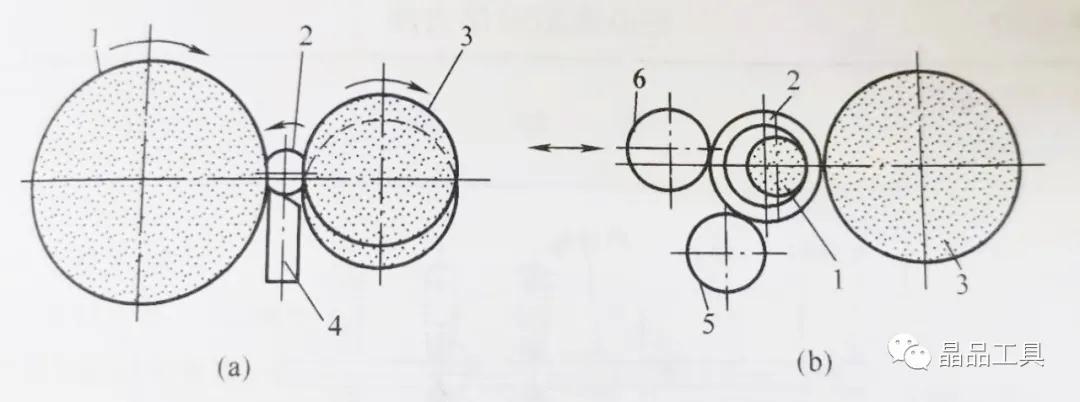
无心磨削的形式
(a)外圆无心磨削 (b)內圆无心磨削
1—磨削轮(砂轮) 2—工件 3—导轮 4—托板 5—支承轮 6—压紧轮
无心磨削是一种适应大批量生产的高效率磨削方法。外圆磨削公差等级可达IT6~IT7级,磨削圆度公差可达0.0005~0.001mm,表面粗糙度Ra0.1~0.025μm。
无心磨削的特点
(1)磨削过程中,工件中心不定。其位置变化的大小取决于工件的原始误差、工艺系统的刚性、磨削用量及其他磨削工艺参数(工件中心高、托板角等)。
(2)工件的稳定性、均匀性不仅取决于机床传动链,还与工件的形状、质量、导轮及支承的材料、表面状态、磨削用量和其他工艺参数有关。
(3)外圆磨削支承刚性好,內圆磨削用支承刚性也好,可取较大的背吃刀量,而且砂轮的磨损、补偿和定位产生的误差对工件直径误差影响较小。
(4)生产率高。外圆磨削和內圆磨削上下料时间重合,如加上一些附件,很容易实现磨削过程自动化。
(5)外圆磨削易实现强力磨削、高速磨削和宽砂轮磨削。
(6)內圆磨削多数情况下只能加工可放在滚柱上滚动的工件,特别适应磨削薄壁工件,加工的内孔与外圆的同轴度要求较高。
(7)不能修正孔与轴的轴线偏移,工件同轴度要求较低。
(8)机床调整比较费时,单件小批量生产不经济。
影响无心外圆磨削质量的要素
(一)磨削砂轮
1.砂轮形状
砂轮形状直接影响磨削质量、生产率及自身消耗。贯穿磨削时,一般要求砂轮形状适应进料—预磨—精磨—光磨—出料等过程。下图是贯穿法磨削用砂轮形状。当背吃刀量大时,l1、l2长些,角γ1、γ2大些;反之,γ1、γ2小些而l3长些。
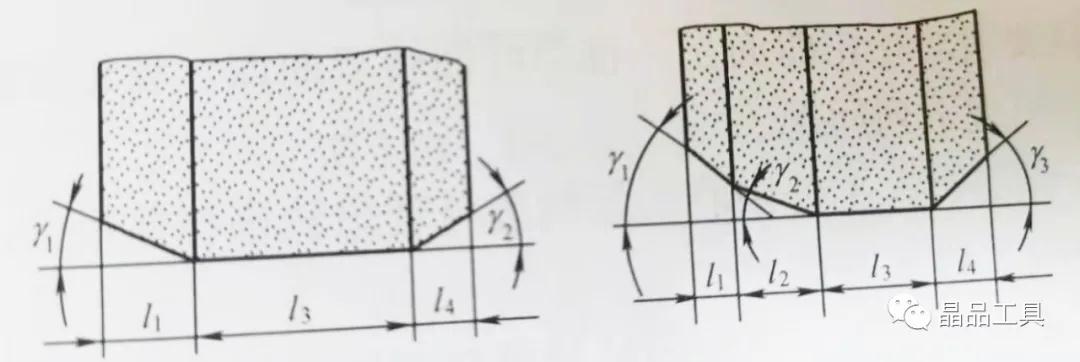
贯穿法磨削砂轮
下图是宽砂轮,l1是进料区,10~15mm,l2是预磨区,根据磨削用量确定。L3是精磨或光磨区,粗磨时5~10mm。A等于最大磨削余量,Δ1为进料口,约0.5mm,Δ2为出料口,约0.2mm。
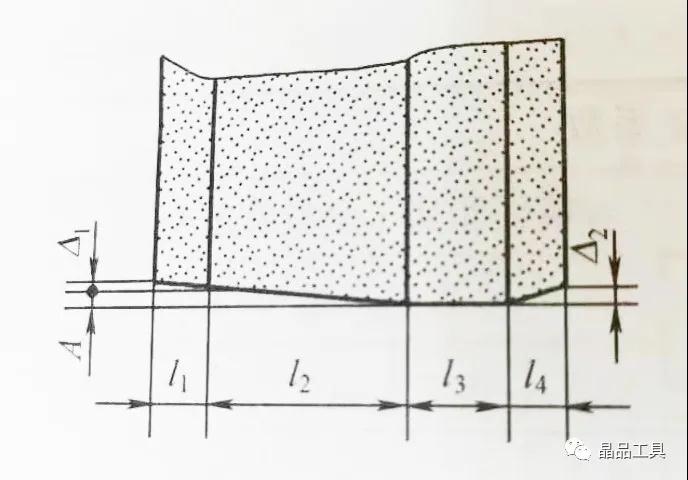
宽砂轮形状
2.砂轮特性
砂轮特性常和导轮结合起来考虑。砂轮和导轮最大外径及宽度是由机床决定的。贯穿法磨削时,砂轮与导轮同宽;切入法磨削时,一般也相同;磨圆球面工件时,导轮应窄一些,但一般轮宽不小于25mm.以M1080无心磨床为例,砂轮直径500mm,用贯穿法磨削时,砂轮和导轮宽度为150~200mm。用切入法磨削时,砂轮和导轮比工件待磨长度长5~10mm。
砂轮的磨料、粒度、硬度、几何级选择与一般外圆磨削基本相同。但通常比一般外圆磨削选得稍硬一些;无心贯穿法磨削时比切入法磨削时稍软一些;多砂轮磨削时,直径小的砂轮稍硬一些。导轮比磨削砂轮要硬一些,粒度要细一些。