(1)合理选择磨削用量
1)砂轮速度υs增高,磨削温度相应上升,越易发生烧伤。
2)背吃刀量ap越大,工件表面温度越高,因此宜选用较小的ap,但ap过小时,则导致磨削时滑擦与刻划的能量增加,反而易引起表面烧伤。
3)工件速度υw增高,产生的热量增加,但随着υw增加磨削热源在工件表面上移动的速度加快,散热的条件改善,故烧伤情况减轻。
在生产实践中较有效果的措施是减小背吃刀量ap,适当减小砂轮速度υs及增加工件速度υw来减小工件表面烧伤和裂纹。
(2)正确选择砂轮。选用较粗的磨粒,采取粗修整,降低砂轮的硬度,控制砂轮磨损和防止砂轮粘着与堵塞,均能有效地降低磨削温度。其中砂轮硬度的合理选择对磨削表面烧伤影响最大,在磨削导热性差的材料、空心薄壁工件、工件与砂轮接触弧较长时,都应选较软的砂轮,以发挥砂轮的自研作用。
磨料的选择也有很大影响。如磨硬质合金工件,采用碳化硅砂轮,多数工件都出现烧伤现象。若选金刚石砂轮磨削,则磨削力小,干磨时摩擦因数小,故磨削区发热量小。
在产生磨削热多和砂轮与工件接触面积大的情况下,可采用大气孔砂轮或表面开槽砂轮。这种砂轮具有不易堵塞、切削能力强和散热快等优点。
(3)提高冷却润滑效果。
(4)及时修整砂轮
(5)采用低应力磨削工艺。采用低应力磨削,工件表面可获得低的残余拉应力,减少表面烧伤与裂纹。所谓低应力磨削,即在表面0.025mm以下深度时,残余应力小于120Mpa。下图所示为低应力磨削与普通磨削的残余应力比较图。
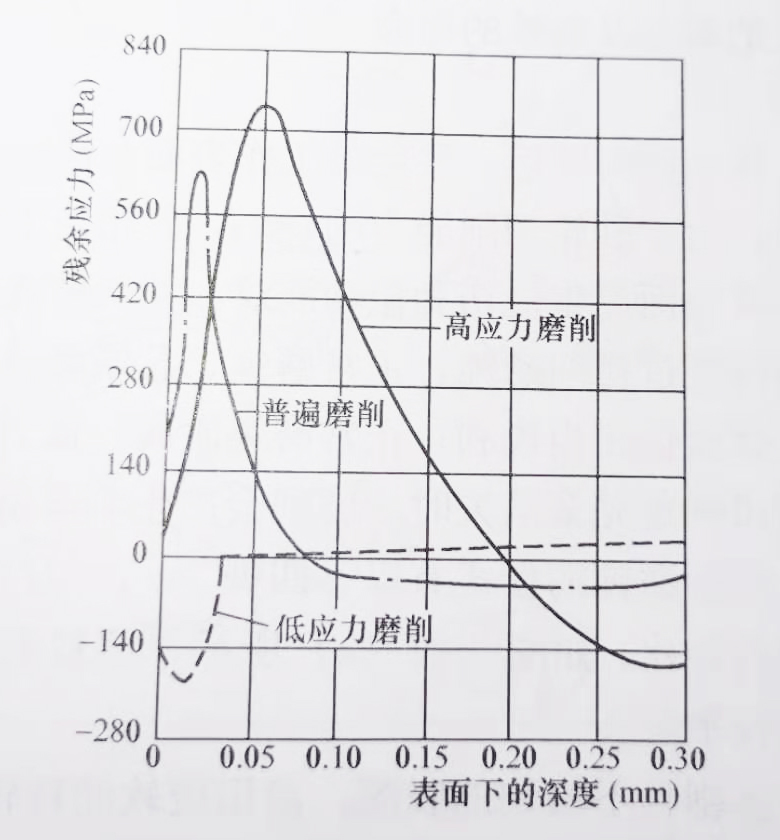
不同磨削方式对残余应力的影响
低应力磨削砂轮速度要低,砂轮硬度要软,横向进给量要小,下表为低应力磨削与其他磨削主要参数比较。
低应力平面磨削与其他磨削主要参数比较
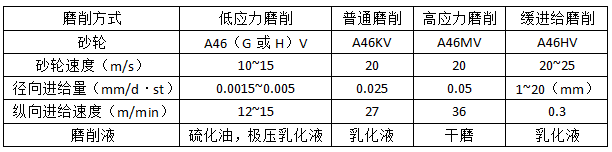
低应力磨削适于磨削高强度和高温合金等精密零件,但磨削效率低。因此,磨削余量要小,一般余量取0.25mm,其中先以fr=0.01~0.02mm/st,切除0.2mm余量,然后再以0.005~0.01mm/st切除剩下的余量。近年来采用CBN砂轮,由于能较长时间保持锋利的切削刃,磨削效率有所提高。