研磨的特点
(1) 尺寸精度高。研磨在低速、低压力下磨除一层极薄金属层,工件变形和表面变质层很轻微,可稳定获得高精度表面。其尺寸精度可达0.025μm。
(2) 形位精度高。圆度可达0.025μm,圆柱度达到0.1μm。
(3) 表面粗糙度值低。研磨能均匀地切掉工件表面的凸峰,降低表面粗糙度,其Ra可达0.008μm。并能使两个零件的接触面达到精密配合。
(4) 不能提高工件各表面间的位置精度。
(5) 工件表面耐磨性提高。因为凸峰被磨平,有效接触面积增大。
(6) 工件表面疲劳强度提高。
(7) 设备简单、制造方便。
(8) 适应性好。可单件手工生产,也可成批机械化生产。可加工钢材、铸铁、各种有色金属,亦可加工硬脆的玻璃、陶瓷等非金属。
研磨的分类
按研磨剂使用的条件,研磨可分为如下三类。
(1) 湿研(又称敷料研磨)。把研磨剂连续加注或涂敷于研具表面,磨料在工件与研具之间不停地滚动或滑动,形成对工件的切削运动。其金属切除率高,可达干式研磨的5倍以上。但在加工表面几何形状和尺寸精度方面不如干式研磨,因此多用于粗研和半精研。
(2) 干研(又称嵌砂研磨或压砂研磨)。在一定压力下,将磨粒均匀地压嵌在研具的表层中,嵌砂后进行研磨加工。这种研磨方法可获得很高的加工精度和低的表面粗糙度值,但效率低。
(3) 半干磨。类似湿磨,采用的研磨剂是糊状的研磨膏,粗、精研均可采用。
根据加工表面形状特点,还可分为平面、外圆、内孔、球面、螺纹、成形表面的研磨和啮合表面轮廓研磨等。
按精密程度可分为普通研磨和超精密研磨。超精密研磨又可分为振动研磨和电解研磨。
研磨机理
研磨是由游离的磨粒通过研具对工件进行微量切削的过程。在被加工表面和研具之间置以游离磨料和润滑液,使被加工表面和研具产生相对运动并加压,磨料产生切削、挤压等作用,从而去除表面凸处,使被加工表面精度得以提高,表面粗糙度参数值得以降低。研磨加工模型如下图所示。
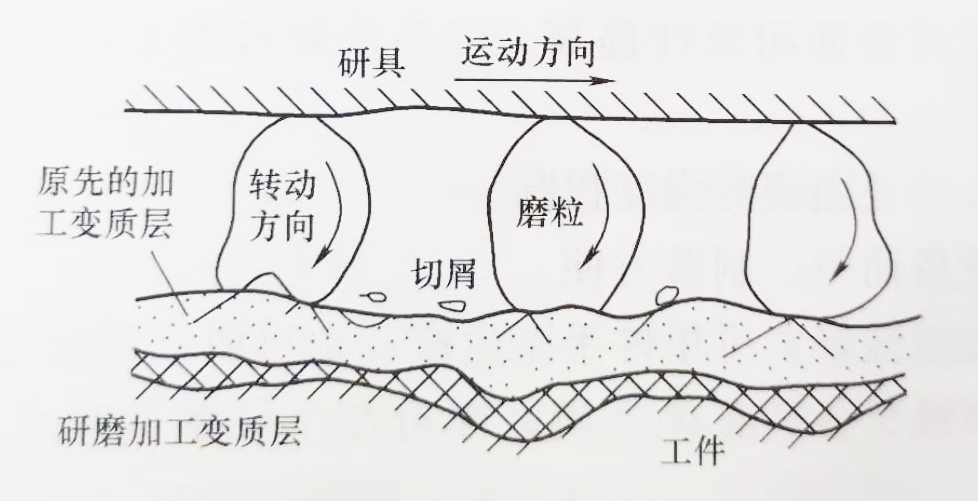
研磨加工模型
研磨机理可归纳为以下几种作用:
(1) 磨粒的切削作用。磨粒的切削作用在不同的条件下有不同的方式。在研具较软、研磨压力较大的情况下,磨粒可镶嵌到研具上,产生刮削作用,这种方式有较高的效率。在研具较硬(如淬硬合金钢)、研磨压力较大的情况下,磨粒不能嵌入研具,而是在被加工表面和研具之间滚动,以其锋锐的尖角进行切削。
(2) 塑性变形。磨料挤压被加工表面的粗糙峰部,在塑性变形及流动中使工件表面峰谷趋于熨平或在反复变形中产生加工硬化,最后断裂而形成细微切屑。
(3) 化学作用。当采用氧化铬、硬脂酸或其他研磨剂时,工件表面会形成一层极薄的氧化膜,这层氧化膜很容易被磨掉而不伤基体。在研磨中氧化膜会不断地迅速形成,又不断被磨掉,从而加快了研磨过程,使表面粗糙度降低。