金刚石刀具的性能优势
1.单晶金刚石刀具的性能优势
(1)单晶金刚石刀具具有极高的硬度(10000HV),从而获得良好的耐磨性;
(2)单晶金刚石刀具的切削刃可以磨得非常锋利,切削时不宜粘刀和产生积屑瘤,可进行超薄切削和超精密加工;
(3)摩擦系数低,加工时变形小,可减小切削力;
(4)刃口在800倍Nomarski(尼康)显微镜下观察无缺陷,加工有色金属时表面粗糙度可达Rz0.1~0.05μm,被加工工件的形状精度控制50nm以下;
(5)晶品超硬精选的单晶金刚石刀具颗粒,一致性好,使用寿命是硬质合金刀具的100倍,甚至几百倍。
2.PCD刀具的性能优势
(1)PCD的硬度可达8000HV,为硬质合金的80~120倍;
(2)PCD的导热系数为700W/mk,为硬质合金的1.5~9倍,甚至高于PCBN和铜,因此PCD刀具热量传递迅速;
(3)PCD的摩擦系数一般为0.1~0.3(硬质合金的摩擦系数为0.4~1),因此PCD刀具可显著减小切削力;
(4)PCD的热膨胀系数仅为0.9*10-6~1.18*10-6,仅相当于硬质合金的1/5,因此PCD刀具热变形小,加工精度高;
(5)PCD刀具与有色金属和非金属材料件的亲和力很小,在加工过程中切屑不易粘结在刀刃上形成积屑瘤。
单晶金刚石/PCD/CVD刀具的区别
1. 性能区别
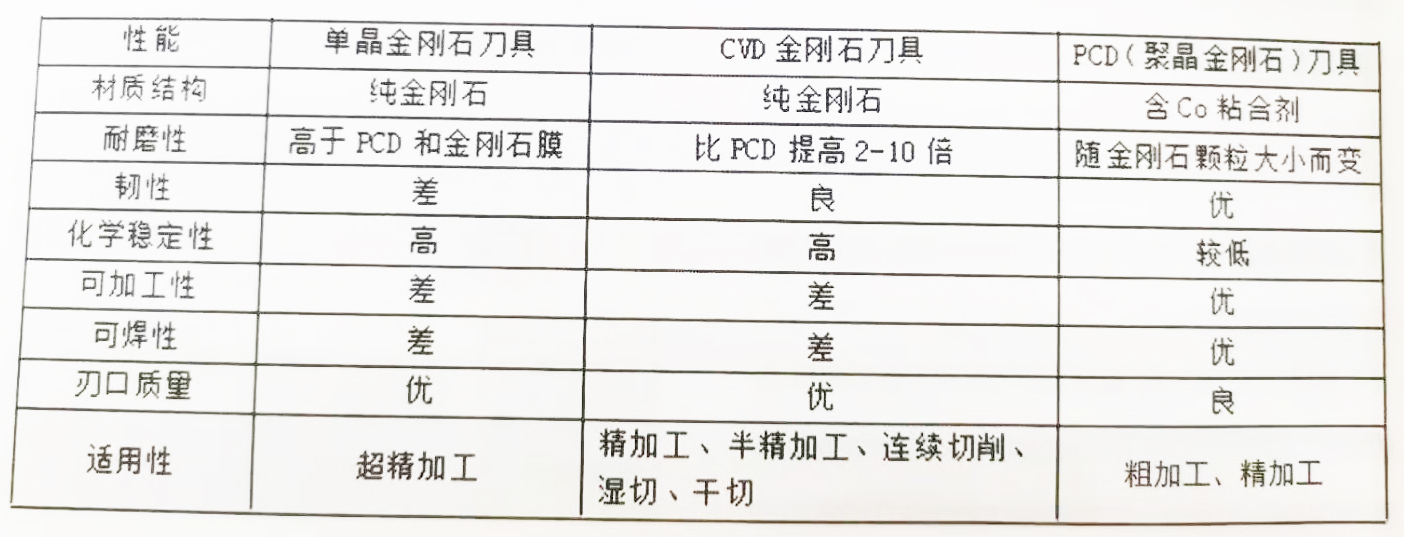
2. 应用区别
单晶金刚石几乎专用于高精密的精加工,其极薄切削能力可确保获得极高的尺寸精度。PCD刀具最适合加工铝和其他韧性较好的非铁合金(如铜、黄铜和青铜),以及具有高磨蚀性的复合材料(如石墨、碳-碳材料、加碳酚醛、玻璃纤维和多孔密封材料)。
PCD和CVD金刚石可用于许多相同的加工领域,但PCD更合适用于粗加工以及对刀具断裂韧性要求较高的加工场合。CVD金刚石更擅长精加工、半精加工和连续车削加工,这是因为其具有优异的耐磨性和高硬度,可以加工出更精密的工件。
目前单晶金刚石刀具和PCD应用最为广泛,CVD厚膜刀具目前由于磨削工艺限制了其推广使用。
3. 刀具刃口及加工区别
A: 聚晶金刚石(PCD)与单晶金刚石刀具在金显微镜下的状况,左下图可明显看出刀刃边缘会呈现锯齿状,而右图则平顺光滑。
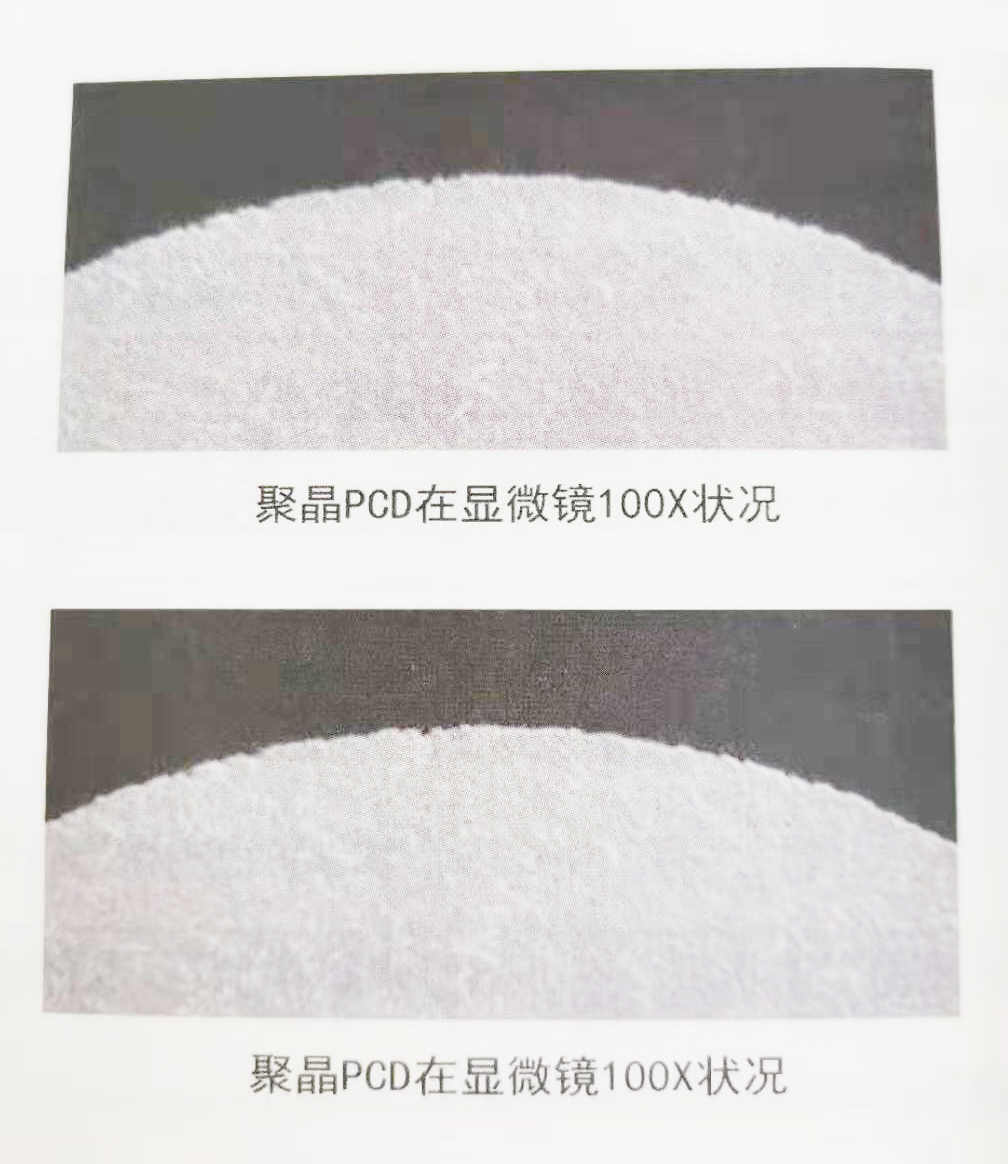
B: 在加工方面的差异性
聚晶金刚石(PCD)刀具的刀刃由许多微细晶体所构成,因此在进行加工车削,被加工物表面也会呈现一颗颗小晶粒所造成的痕迹。单晶金刚石刀具可以将刀刃完美的状态,直接复制在被加工物上。
左图为聚晶金刚石(PCD)刀具加工工件表面,右图为单晶金刚石刀具加工工件表面。
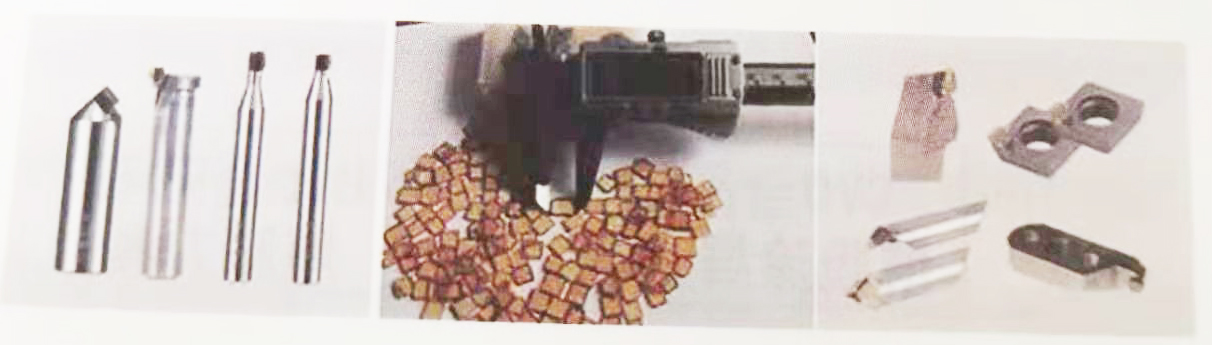