高速磨削砂轮要求砂轮基体的机械强度必须能承受高速磨削时的切削力以保证高速磨削时的安全可靠性。这就要求砂轮中的磨粒突出高度大且结合剂有高的耐磨性。
高速磨削砂轮的磨粒主要是金刚石和立方氮化硼,所用的结合剂有多孔陶瓷和电镀镍。随着高速磨削的进一步推广和科研的深入,新型的磨粒和结合剂也在不断出现。
为了保证砂轮在整个寿命中保持锋利,砂轮的结构还需有利于磨粒分裂,维持自砺过程。要达到砂轮自锋利的目的,除了尽量降低结合剂的比例外,还要优化磨粒的空间分布。下图是带自然孔的普通砂轮与带人造孔的新型砂轮结构的对比,后者磨粒间的气孔由发孔剂生产,在相同的面积内,可以明显地减少磨粒的数量。当切削力不变时,分摊在每一磨粒上的力相应增加,利于促进磨粒分裂和砂轮自砺的形成。通过计算机程序可算出各种磨粒分裂时作用在单个磨粒上的力,从而可准确地确定结合剂的比例。
金刚石砂轮的特性与一般砂轮不同的是,它另有金刚石浓度和金刚石料层尺寸的规定。由于金刚石是一种比较昂贵的材料,制造这种磨具时,磨具的非工作部分是没有金刚石的。金刚石料层是指砂轮砂轮在磨削加工时可用的尺寸,这个尺寸部分是金刚石和结合剂制成。一般的做法是把这个部分直接压在一个非工作的“基体”上,但是也有将这个部分镶在“基体”上的。
金刚石砂轮的磨料,有天然金刚石和人造金刚石两种。天然金刚石晶粒表面光滑,抗冲击性能好。而人造金刚石晶粒表面粗糙、脆性大,两类金刚石的磨削性能各具特色。对受冲击载荷的场合,采用天然金刚石较好,对于一般磨削场合,采用人造金刚石的效果更佳。天然金刚石和人造金刚石的硬度都极高,颗粒棱角锋利,且不易磨损,所以金刚石砂轮的切削性能很好,切削效率高,切削力小,发热量少,磨削温度低。
根据我国特点,目前生产的金刚石砂轮主要是以人造金刚石作磨料,共分四型,即JR1、JR2、JR3、JR4,各种型号的磨粒由于颗粒形状和性能的不同,用途也不同。
金刚石砂轮结合剂,常用的金属结合剂(M)、树脂结合剂(B)、陶瓷结合剂(V)三种。不同结合剂砂轮的浓度范围如下表。金属结合剂砂轮使用寿命长,可以承受较大的磨削载荷,但切削效率不如树脂结合剂的高。树脂结合剂砂轮磨削效率高,加工表面质量好,砂轮容易修整。陶瓷结合剂金刚石砂轮磨削效率高,磨损小,能很好地保持砂轮的几何形状。
不同结合剂的浓度范围
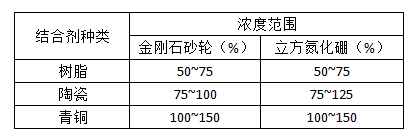